Why plastic extrusion is the best choice for mass production
Why plastic extrusion is the best choice for mass production
Blog Article
Key Advantages and Considerations of Implementing Plastic Extrusion in Your Projects
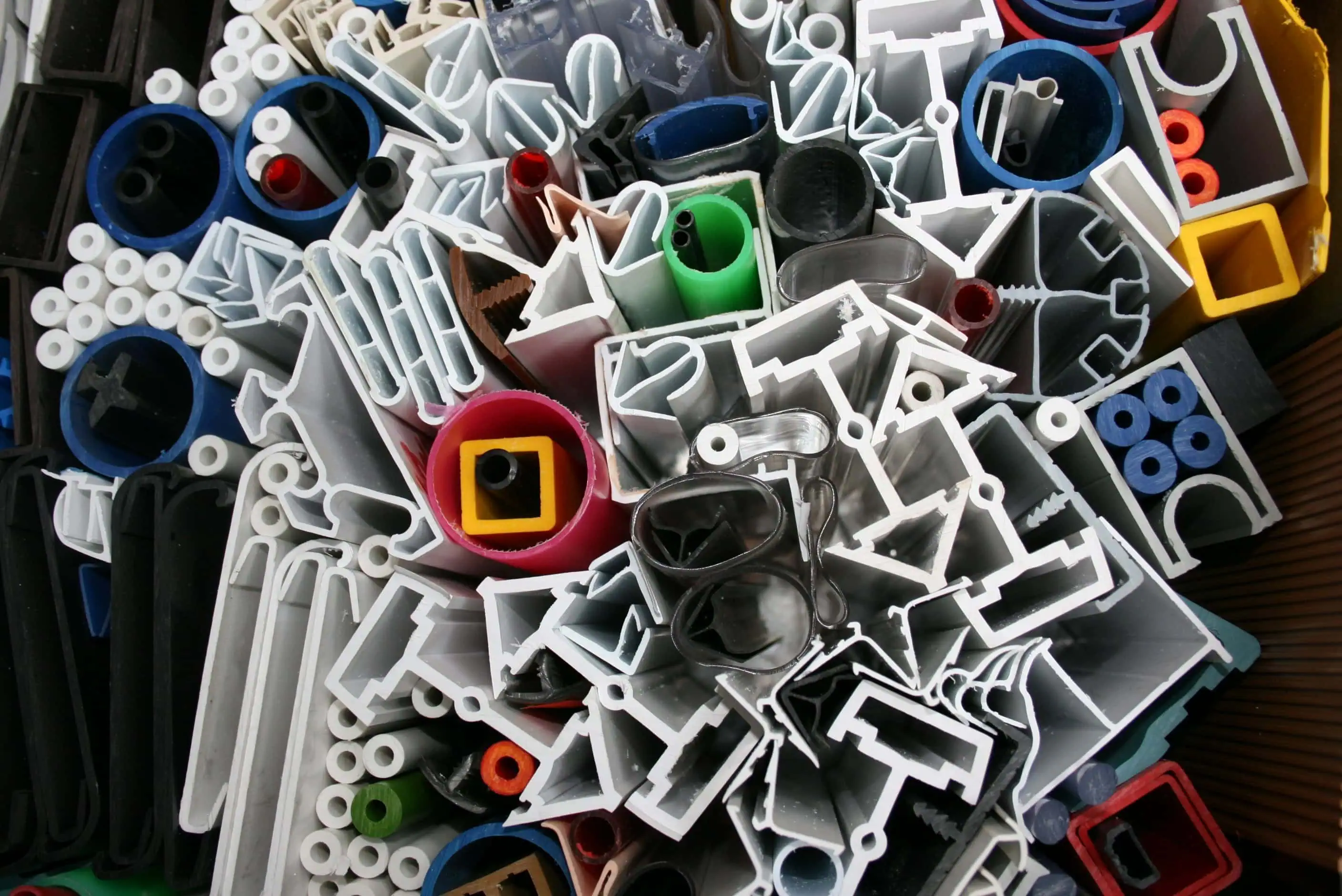
Recognizing the Basics of Plastic Extrusion
Plastic extrusion, a staple in the manufacturing market, is a process that entails melting raw plastic product and reshaping it into a continuous account. This account, once cooled, can be reduced into preferred sizes or coiled for later usage. The appeal of plastic extrusion hinges on its flexibility. A large range of items, from piping to home window structures, can be produced. The procedure needs an extruder, an intricate equipment with a heated barrel, a rotating screw, and a die at the end. The plastic product, in the form of pellets, is fed into the extruder, where it's thawed and forced with the die, taking its form. The option of plastic and the design of the die establish the product's features.

The Economic Benefit of Plastic Extrusion
The financial advantage of plastic extrusion lies predominantly in 2 locations: affordable product production and useful production speeds. With plastic extrusion, services can produce high volumes of material at a reduced price contrasted to various other approaches. Furthermore, the process flaunts a remarkable production speed, significantly reducing time and further boosting its financial feasibility.
Economical Material Production
A substantial benefit of plastic extrusion is its remarkable cost-effectiveness. In addition, the extrusion procedure permits for a high degree of accuracy in shaping the plastic, minimizing the demand for pricey post-production modifications or adjustments. All these aspects make plastic extrusion a very cost-effective selection for lots of jobs, offering an eye-catching balance between cost and efficiency.
Beneficial Manufacturing Speeds
While preserving the cost-effectiveness of the products, one more notable advantage of plastic extrusion depends on its fast production rates. This effectiveness in the manufacturing process is credited to the continual nature of the extrusion procedure, allowing for high-volume manufacturing in a reasonably brief time period. The rate of manufacturing directly correlates to a decrease in labor prices and a rise in output, therefore enhancing the total financial feasibility of the procedure. In addition, the hectic manufacturing does not jeopardize the high quality of the end product, guaranteeing regular and trustworthy outcomes. This mix of quality, cost-effectiveness, and rate underscores the substantial economic benefit of implementing plastic extrusion in different tasks.
Flexibility and Personalization: The Strengths of Plastic Extrusion
One of the noticeable staminas of plastic extrusion lies in its versatility and customization possibility. These top qualities open up the door to unrestricted style opportunities, offering makers the ability to customize items to particular needs. This enhanced level of modification not only enhances item functionality yet likewise substantially increases product individuality.
Unlimited Layout Opportunities
Plastic extrusion beams in its capacity to offer almost infinite design opportunities. This approach gives liberty to develop intricate forms and complex accounts, a feat hard to achieve with other fabrication techniques. Owing to the liquid nature of molten plastic, the procedure is adaptable enough to yield a diverse variety of dimensions, forms, and next dimensions. The plastic can be controlled to match special specs, enabling the production of customized geometries and meeting certain customer demands. Plastic extrusion can deal with a selection of plastic kinds, increasing its application range. This adaptable technique, as a result, offers a variety of sectors from building to auto, packaging to electronics, and past. With plastic extrusion, the style possibilities are essentially countless.
Enhancing Item Originality
The versatility of plastic extrusion can significantly enhance product individuality. This process enables designers to try out different forms, dimensions, and shades, providing the liberty to develop unique items that stand apart in the marketplace. It is this customization that offers an unique identification per product, differentiating it from its rivals.
In enhancement to its aesthetic advantages, the customizability of plastic extrusion additionally supplies functional benefits. Developers can customize the residential or commercial properties of the plastic according to the specific demands of the application, improving the product's functionality. For circumstances, they can make the plastic a lot more versatile, more sturdy, or extra resistant to heat, depending on what the item calls for. Therefore, plastic extrusion not just improves product originality however also its energy and marketability.
Style Limitations in Plastic Extrusion: What You Need to Know
Just how more can create constraints possibly influence the procedure of plastic extrusion? While plastic extrusion is functional, style limitations can reduce its benefits. Specific complex styles might not be possible due to the restrictions of the extrusion process, possibly limiting the development of intricate accounts. The process is less appropriate for multi-chambered or hollow structures. Additionally, the extrusion process may not constantly provide the desired surface area coating, specifically for those calling for high gloss or optical clearness. Material choice can also pose obstacles, as not all polymers are ideal for extrusion. High-temperature resistant plastics, for instance, might provide difficulties. Recognizing these restrictions is vital for reliable execution of plastic extrusion in your projects. plastic extrusion.
Examining the Ecological Effect of Plastic Extrusion
While recognizing layout constraints is a substantial facet of plastic extrusion, it is just as important to consider its environmental ramifications. The procedure of plastic extrusion entails melting plastic products, potentially launching harmful gases right into the atmosphere. Even more, the resulting items are commonly non-biodegradable, adding to land fill waste. Nonetheless, developments in innovation have permitted even more environmentally-friendly methods. Using recycled plastic materials in the extrusion procedure can minimize environmental impact. In addition, creating eco-friendly plastic choices can help reduce waste problems. Evaluating these ecological elements is important when implementing plastic extrusion jobs, ensuring an equilibrium between effectiveness, cost-effectiveness, and environmental obligation.
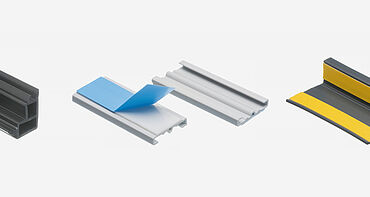
Study: Successful Projects Using Plastic Extrusion
Success tales in the field of plastic extrusion abound, showing both the versatility and effectiveness of this production procedure. One remarkable instance is the creation of PVC pipelines made use of in modern-day pipes. This procedure includes melting plastic and forming it into a continual tube, providing significant cost and resilience benefits. One more successful case is the manufacturing of plastic movie for product packaging and agriculture. Via extrusion, manufacturers can create highly adjustable, slim, and durable movies. Automotive sectors additionally profit, making use of extruded plastic for components like trim or seals, boosting lorry longevity. These instances highlight plastic extrusion's important role in different markets, proving to its flexibility, cost-effectiveness, and trusted result.
Final thought
In verdict, plastic extrusion supplies a efficient and economical technique for generating complex shapes with marginal waste. While it provides countless advantages such as cost-effectiveness and versatility, it's crucial to think check my source about potential style constraints and ecological results. Applying recycled or naturally degradable products can mitigate these problems, enhancing sustainability. Integrating plastic extrusion into jobs can bring about successful results, as shown by various instance studies.
Plastic extrusion, a staple in the manufacturing sector, is a procedure that includes melting raw plastic product and improving it into a continuous profile. Plastic extrusion can deal with a selection of plastic types, expanding its application extent.Just how can develop limitations possibly impact the procedure of plastic extrusion? The process of plastic extrusion involves melting plastic products, potentially releasing damaging gases into the setting. Using recycled plastic products in the extrusion procedure can reduce environmental impact.
Report this page